Keywords |
Electro Coagulation, CPN, Robotics, Oil Spills |
INTRODUCTION |
主要包括电化学反应an anode, a cathode, battery connections and an electrolyte for the passage of charge. Electro coagulation is an electrochemical process that has a sacrificial anode and an inert cathode with the impure water as an electrolyte. A sacrificial anode is an electrode that corrodes or has a reduction in its weight during the reaction. The anode can be an array of metals chosen to meet the needs of a specific impurity. Anode metal ion forms a hydroxyl ion on reacting with water which reacts with more hydroxyl ion present in water to form a pentavalent poly hydroxyl ion which has a high charge and an increased mass. These heavy ions attach themselves to the impurity particles present hence losing their charge and forming sediment. Colloidal impurities follow a different mechanism than floating impurities such as oil. An emulsion has impurity in direct contact with the ions from anode. To sediment a floating impurity the wander ValâÂÂs force between the molecules has to be neutralized. The ions from anode slowly neutralize these forces and cause sedimentation. Turbulence can often assist this process; alternatively the oil water mixture can be mixed at a high rpm in a magnetic stir for a long period of time to form an emulsion. The cathode is inert which means it does gain or lose mass, it reacts with water forming hydrogen bubbles. This is an important process in electro coagulation, though coagulation is the primary process, flotation takes place simultaneously due to the hydrogen bubbles evolved at the cathode. The floc formed at the surface can be easily skimmed away contains impurities that do not sediment easily. There are different methods to conduct the process: continuous, batch, overflow. Every method has its benefits and drawbacks. Overflow type reactor design was studied and results were documented. The overflow type demands a high current density as it has short interaction time between the water and electrodes. Current density is an important factor for the process, maintaining a correct current density can ensure the propagation of the desired reaction whereas the wrong current density can suppress the desired reaction and promote an otherwise undesired reaction. The range can be anywhere between 2-20 ampere meter square. |
ELECTROCHEMICAL ASPECT |
Factors that matter |
• Type of electrode |
• Choice of metal for electrode |
• Dimensions of electrodes |
• Distance between electrodes |
• Electrode configuration |
• Time of reaction |
• Current density |
• Type of reactor configuration |
• pH of processed water |
• Weight loss of anode |
• Sedimentation behavior and time |
• Development of rector |
The reactor is an overflow type; water enters through the top by penetrating the surface tension and enters the reactor where the electro coagulation takes place. The overflow treated water is pumped out to the sedimentation chamber. The reactor had a supply of lake water being funnelled in through a pipe connected at the base. The water enters through the bottom and the level keeps rising till it overflowed from the top. The time that the water level takes to rise from the bottom to the point of overflowing was the time of reaction. The electrodes are connected to the battery throughout the procedure and provided an initial current of 20 amps. This mono polar overflow reactor was an improvement from the |
 |
previous versions as the inter electrode distance was less, current density was high, the time of the reaction was very less compared to the earlier experiments. The reaction time was 40- 60 seconds in contrast to the 40- 60 minutes taken earlier. |
INTEGRATION OF DESIGN |
The final design was an integration of all the experiments conducted before. The experiments were done to observe the correct specifications for the formation of a reactor. Aluminium electrodes (15 x 2x0.3cm length, breadth and thickness). |
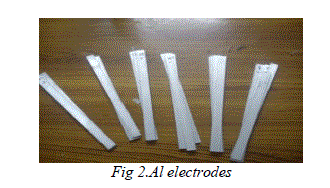 |
ELECTRODE PLACEMENT |
Four electrodes are connected in a mono polar configuration, there are protective blocks of wood placed between the electrodes to maintain shape and prevent short circuiting. The electrodes are kept at a distance of 3 mm from each other and are fixed on a wood platform. The small distance between them speeds the rate of reaction. Below figure shows the electrode placement within the PVC pipes. |
 |
EXTERNAL CHASSIS |
The external chassis has a connector for taking output. The support beams on the sides provide |
 |
strength to the structure and the upper ring allows for the design to be submerged and break surface tension. Material is sheet metal of higher thickness, approximately 0.1mm. |
 |
The electrode assembly is placed inside the chassis which is painted inside as well as outside with protective paint. The PVC pipes are of 4 inches diameter and have a pipe connected at the base of them to provide input to the over flow type reactor. The electrode connection is mono polar, cable used is a 22 gauge copper insulated wire. |
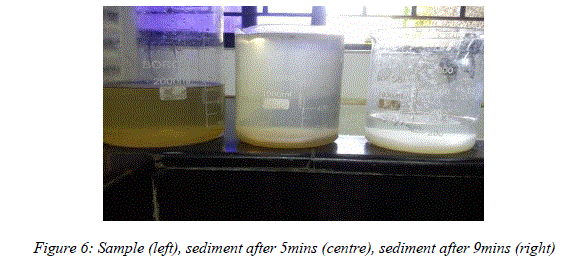 |
PH ANALYSIS |
The samples taken were analysed in the micro biology laboratory in NIOT ( National Institute Of Ocean Technology)to determine the behaviour of pH before the reactor, after the reactor and after allowing some time for sedimentation. It was found that the pH of the sample approached 7 to 8. |
 |
TYPE OF METAL |
When the chassis is to be submerged in water the nature of metal is important. High grade sheet metal was chosen to make the body of the reactor which was covered with rubber to insulate the body to any possible electrical charge. The structure shown below is to be used to navigate the reactor and hoist it in and out of water. The top of the structure has a stand to mount a wireless camera. The platform the camera is placed on can be rotated 360 degrees using a motor hence providing a complete sight of the surroundings. |
The external chassis comprises of a design to navigate the reactor, to lower the reactor in water and to lift it up. |
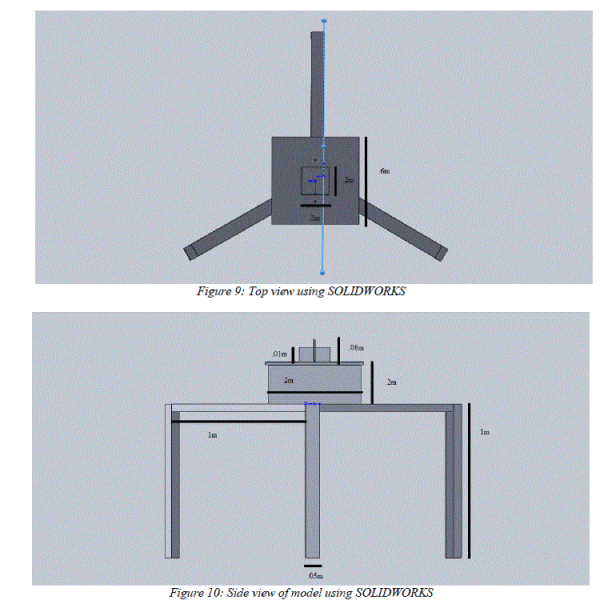 |
 |
BATTERY BOX |
The box mounted on the chassis is a water proof battery box following standards LP 65 with connectors to take out output terminals from the battery |
 |
The inner side of the box is lined with insulating casket and has a proper sealing and locking mechanism so that no water from outside enters the box. The connector has battery terminals on the inside and has a higher gauge and wire count than ordinary twisted pair cable; the connector ensures a safe connection between the load and battery. |
FLOAT |
The floats attached are buoys to accommodate the entire weight of the system including the weight of motors, battery, battery box and all the other components. The total weight of the system must be less than the buoyâÂÂs buoyancy for successful flotation. The weight of the body is reduced by 1/7th its weight in water. |
 |
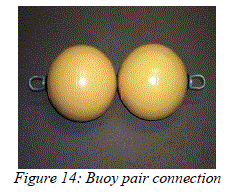 |
AIR RESISTANCE |
The air resistance was also to be considered because the system may float away from its target site in event of fast winds blowing, hence the vertical height above water is kept minimal and the dimensions of the body above water were kept optimal so that there is reduced effect of winds on the system. The centre of gravity is maintained on the axis passing through the centre of the system by its symmetric design to provide good stability. |
 |
SOFTWARE ASPECT |
Coloured Petri Nets (CPN) |
A simulation model was developed using coloured Petri nets to demonstrate an overview of the working of the system. The simulation of CPN is based on triggering of inputs and demonstrating the resultant action impact on the system, it is parallel process simulation software where the triggering of one input has response from different sub systems, all these processes can be observed to code a micro controller for performing similar actions in real time situations. Coloured Petri Nets is chosen as the platform for creating a simulation model as the token transfer in CPN is clearly understandable along with it treating all values in 0 or 1, which creates a direct colliery with the working of a micro controller. CPN adds the concept of coding, graphical interface and Petri nets to produce a system which has powerful primitives and has a vast potential. The obtaining of a hexadecimal code from a CPN simulation is in its path of a commercial release and it will improve current modelling schemes as CPN will greatly reduce the processing time in micro controllers. The simulation results and further explanation is given in paper titled „Development of mobile surface water filtration system using CPN simulationâÂÂ. |
ELECTRICAL ASPECTS |
Relay Driver |
Relay drivers have a current load limit also they are either single throw or double throw. The current load on the driver for the motors and the electrodes is between 5- 20 amps Specifications: 12v, 74 ohms, 30 amps, double throw |
 |
 |
The pump is for draining the over flown processed water from the reactors into a sedimentation tank. The pump is a submersible DC pump and is fixed at the base platform on which the reactors are placed. |
 |
The float level sensor acts as a switch to the circuit, when the level is low the circuit is broken and no conduction takes place but when the level is high then the float level sensor rises and completes the circuit. To convert this ON/OFF into 0-5V we use a circuit. This circuit gives out 0V when the water is low and 5V when the level is high. This goes into the analog input of the micro controller. |
 |
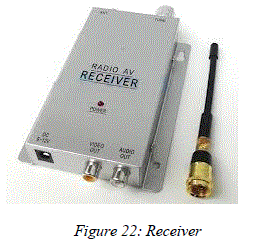 |
The wireless camera is used to provide eyes to the mobile system. The camera transmits AV information through radio waves to the receiver through its antennae. Proper tuning needs to be done on side of the receiver to obtain clear image. |
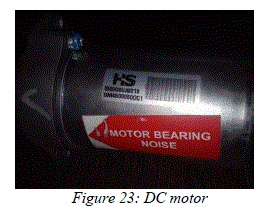 |
Specifications: 12v, 40kg torque, 5 amps current withdrawal, 400 rpm, Brushless motor |
This dc motor is used in propulsion as well as hoisting and lowering the reactor into water. Two motors are used for hoisting and lowering of the reactor to distribute the load so that no motor gets damaged. To prevent the motor from rotating in counter direction in the absence of supply electromagnetic brakes can be used which are activated when the supply to motors is removed. |
CONCLUSION |
By means of the research done it can be established that it is possible to recreate the process of electro coagulation in a down scaled model which can be mounted on a mobile robotic platform. Though this is the first step in a long way to application of mobile electro coagulation reactor based filtration systems the paper establishes a ground idea and opens an entirely new method for tackling problems such as oil spills and chemical dumping. Electro coagulation is applicable to all most types of water impurities, can be optimized to work in short time spans and has very limited draw backs. There is still requirement of more research required to estimate the residual metal ion concentration in the water that is passed through the system to definitively rule out side effects but even then it can be mitigated. |
|
References |
- AashishVatsyayan, B. Hemelatha, “Mobile surface water filtration system”, IJET, 2012.
- AashishVatsyayan, B. Hemelatha, Vimla Juliet, IshwarayaVenkatraman, “Development of mobile surface water filtration system usingCPN simulation”, IJRET, 2013.
- c . Phalakornkule s Polgumhang, w . Tongdaung, Performance of an Electrocoagulation Process in Treating Direct Dye: Batch andContinuousUpflow Processes.
- Abuzaid N.S., Bukhari A.A., Al-Hamouz Z.M. “ Removal of bentonite causing turbidity by electrocoagulation”. J. Environ. Sci. Health,Part A 1998; 33(7): 1341-1358.
- Bioresour , “An Investigation of the electro-coagulation treatment process for the removal of total suspended solids and turbidity from municipal wastewater". Technol. 2008; 99(5): 914-921.
|